The Ultimate Overview to Packaging Machine Repair Work: Maintain Your Operations Running Efficiently
In the realm of packaging, the effectiveness of operations hinges substantially on the reliability of equipment. Understanding the details of product packaging device repair work is essential for maintaining optimal efficiency and decreasing interruptions. Normal maintenance not just expands the life of these machines yet also addresses common concerns that can hamper productivity. As we explore the nuances of troubleshooting and the crucial decision-making process between repair service and substitute, it ends up being clear that a positive strategy can yield substantial benefits. What certain approaches can companies execute to guarantee their product packaging operations stay uninterrupted?
Relevance of Routine Upkeep
Normal maintenance of packaging devices is crucial for making sure optimal efficiency and durability. By executing an organized upkeep timetable, drivers can identify potential issues prior to they rise right into considerable troubles. This positive strategy not only reduces downtime yet also prolongs the life expectancy of the tools, inevitably leading to minimized functional costs.
Regular inspections permit the evaluation of essential components such as belts, seals, and sensors. Dealing with wear and tear quickly protects against unanticipated failings that might interfere with manufacturing and lead to pricey repairs. Additionally, regular upkeep helps make sure conformity with market requirements and regulations, promoting a safe workplace.
Moreover, maintenance activities such as lubrication, cleaning, and calibration significantly boost maker efficiency. Boosted performance equates to consistent product quality, which is important for maintaining customer contentment and brand name track record. A properly maintained packaging equipment runs at optimum speeds and reduces product waste, adding to overall productivity.
Typical Product Packaging Machine Issues
Product packaging equipments, like any kind of complex equipment, can come across a range of usual issues that may hinder their performance and performance - packaging machine repair. One prevalent problem is irregular sealing, which can cause product putridity and wastage if packages are not appropriately sealed. This commonly arises from misaligned parts or worn securing aspects
An additional regular problem is mechanical jams, which can occur due to international objects, used parts, or inappropriate alignment. Jams can cause hold-ups in production and increase downtime, ultimately influencing general efficiency. In addition, electronic breakdowns, such as failure in sensing units or control systems, can lead and interfere with procedures to imprecise dimensions or irregular machine habits.
In addition, issues with item feed can likewise develop, where products may not be delivered to the packaging location consistently, causing disturbances. Wear and tear on rollers and belts can lead to suboptimal performance, requiring immediate focus to avoid further damages.
Comprehending these typical concerns is vital for keeping the honesty of packaging operations, guaranteeing that machinery runs efficiently and efficiently, which in turn aids in meeting production targets and keeping item top quality.
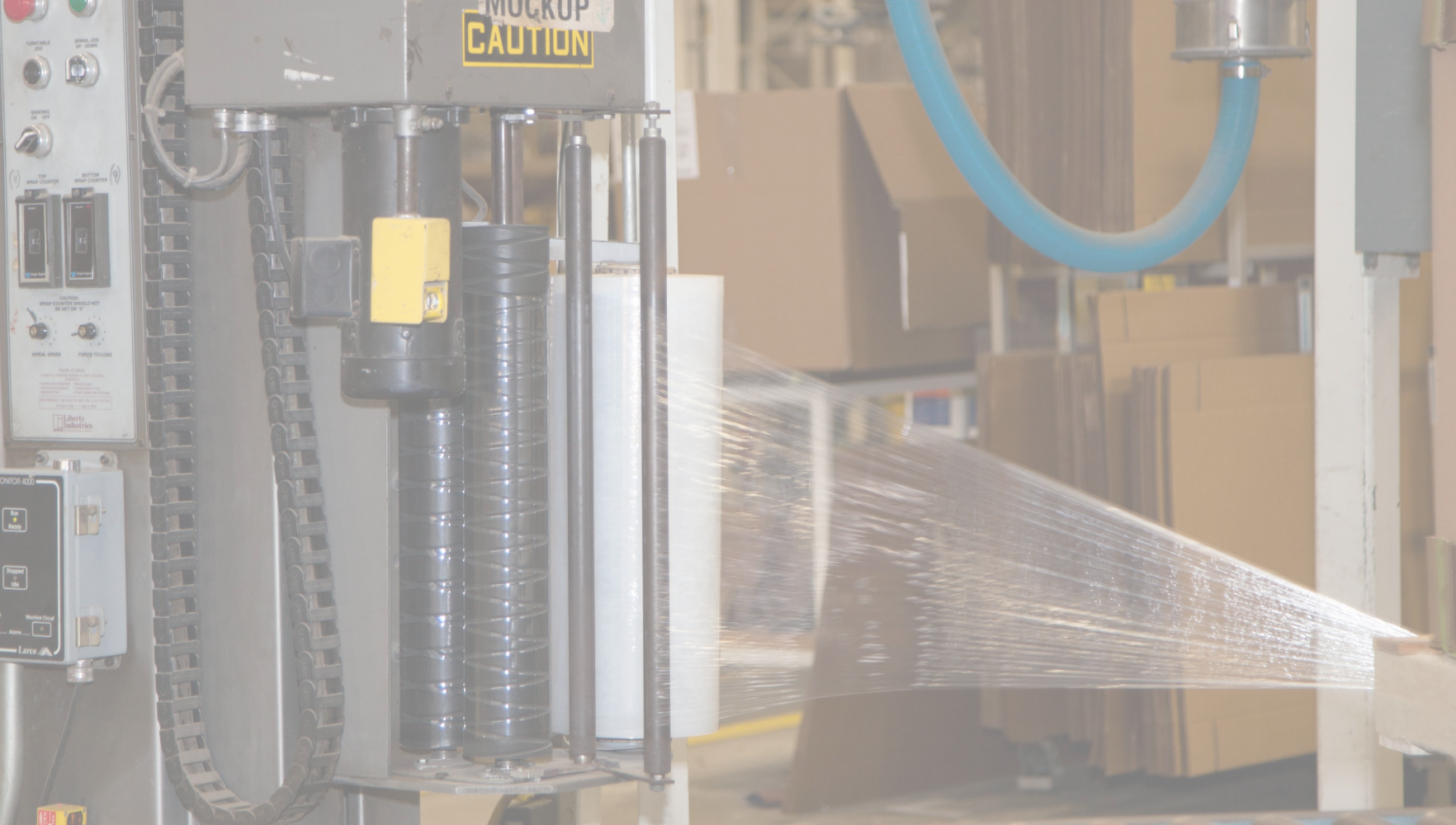
Troubleshooting Techniques
Reliable repairing methods are essential for without delay resolving issues that arise with product packaging devices. An organized technique is important for determining the origin of malfunctions and decreasing downtime. Begin by collecting details concerning the signs observed; this may consist of uncommon noises, functional hold-ups, or error codes displayed on the maker's user interface.
Next, describe the machine's handbook for fixing standards particular to the model in concern. This source can supply useful understandings right into typical concerns and recommended diagnostic actions. Use visual examinations to check for loose connections, worn belts, or misaligned components, as these physical variables usually add to operational failures.
Execute a procedure of elimination by screening private device functions. For circumstances, if a seal is not creating correctly, assess the securing mechanism and temperature level setups to identify if they fulfill operational specifications. File each step taken and the results observed, as this can help in future repairing efforts.
Fixing vs. Replacement Choices
When faced with devices malfunctions, making a decision whether to replace a packaging or repair machine can be a complex and crucial choice. This decision depends upon several crucial elements, including the age of the machine, the extent of the damages, and the forecasted effect on functional efficiency.
Firstly, consider the device's age. Older machines might call for more constant repairs, leading to higher collective costs that can exceed the financial investment in a new device.
Operational downtime is an additional important factor to consider. Spending in a brand-new equipment that uses boosted performance and dependability could be much more click this site prudent if fixing the machine will certainly trigger extended hold-ups. In addition, think about the schedule of components; if replacement parts are tough to come by, it may be a lot more critical to change the device totally.
Inevitably, doing a cost-benefit evaluation that consists of both long-lasting and immediate implications will certainly aid in making an informed decision that lines up with your functional objectives and budgetary constraints. (packaging machine repair)
Preventative Procedures for Longevity
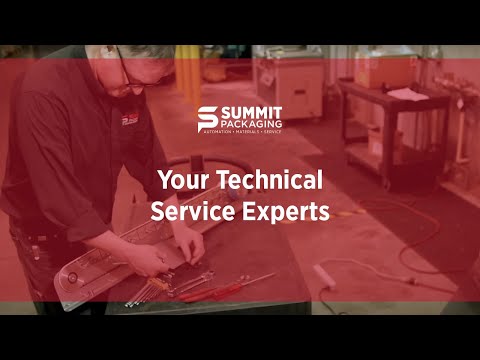
Key preventative procedures consist of routine lubrication of moving components, positioning checks, and calibration of sensors and controls. Developing a cleansing timetable to remove debris and contaminants from machinery can significantly reduce wear and tear (packaging machine repair). Furthermore, checking operational specifications such as temperature and resonance can assist find abnormalities at an early stage
Educating team to identify indications of wear or breakdown is one more critical element of preventative upkeep. Equipping drivers why not try this out with the understanding to do fundamental troubleshooting can result in quicker resolutions and decrease functional interruptions.
Paperwork of upkeep activities, including service documents and examination findings, cultivates liability and helps with notified decision-making pertaining to repair work and replacements. By prioritizing safety nets, companies can ensure their product packaging equipments run at peak performance, eventually bring about raised efficiency and decreased operational expenses.
Verdict
In conclusion, the reliable maintenance and fixing of packaging equipments are vital for maintaining operational performance. Regular maintenance minimizes the threat of typical problems, such as inconsistent securing and mechanical jams, while organized troubleshooting methods help with punctual resolution of breakdowns. Additionally, cautious factor to consider of fixing versus substitute decisions adds to cost-effective administration of resources. By applying safety nets, businesses can boost equipment longevity and make certain undisturbed productivity in product packaging procedures.
Comprehending the complexities of product packaging maker fixing is important for keeping optimum performance and decreasing interruptions.Routine maintenance of product packaging devices is crucial for ensuring optimum performance and long life.Product packaging machines, like any complex equipment, can experience a selection of common issues that might prevent their look here efficiency and efficiency. If repairing the machine will trigger extended hold-ups, investing in a brand-new machine that supplies improved efficiency and reliability might be much more sensible.In verdict, the efficient maintenance and repair of product packaging makers are extremely important for sustaining functional effectiveness.
Comments on “Affordable Packaging Machine Repair Services to Extend Equipment Life”